อุปกรณ์เชื่อม Xinfa มีลักษณะคุณภาพสูงและราคาต่ำ สำหรับรายละเอียด กรุณาเยี่ยมชม:ผู้ผลิตงานเชื่อมและตัด - โรงงานและซัพพลายเออร์งานเชื่อมและตัดของจีน (xinfatools.com)
4. หลุมโค้ง
เป็นปรากฏการณ์การเลื่อนลงที่ปลายแนวเชื่อม ซึ่งไม่เพียงทำให้ความแข็งแรงของการเชื่อมอ่อนลง แต่ยังทำให้เกิดรอยแตกร้าวระหว่างกระบวนการทำความเย็นอีกด้วย
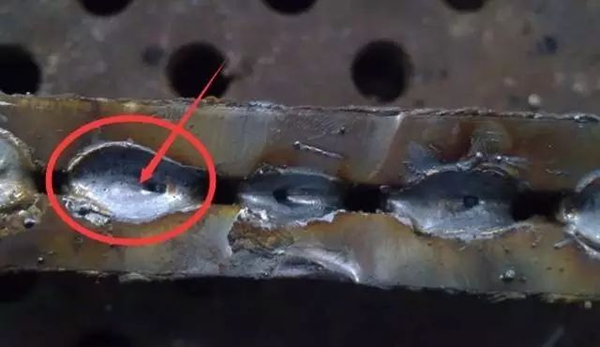
4.1 สาเหตุ:
โดยหลักแล้วเวลาในการดับอาร์คสั้นเกินไปเมื่อสิ้นสุดการเชื่อมหรือกระแสที่ใช้เมื่อเชื่อมแผ่นบางมีขนาดใหญ่เกินไป
4.2 มาตรการป้องกัน:
เมื่อการเชื่อมเสร็จสิ้น ให้อิเล็กโทรดคงอยู่ในช่วงเวลาสั้นๆ หรือเคลื่อนที่เป็นวงกลมหลายๆ ครั้ง อย่าหยุดส่วนโค้งกะทันหันเพื่อให้มีโลหะเพียงพอที่จะเติมสระที่หลอมละลาย ตรวจสอบให้แน่ใจว่ากระแสไฟเหมาะสมระหว่างการเชื่อม ส่วนประกอบหลักสามารถติดตั้งแผ่นสตาร์ทอาร์คเพื่อนำรูอาร์กออกจากการเชื่อม
5. การรวมตะกรัน
5.1 ปรากฏการณ์: สิ่งเจือปนที่ไม่ใช่โลหะ เช่น ออกไซด์ ไนไตรด์ ซัลไฟด์ ฟอสไฟด์ ฯลฯ พบได้ในการเชื่อมโดยการทดสอบแบบไม่ทำลาย ทำให้เกิดรูปร่างที่ผิดปกติหลากหลายรูปแบบ และสิ่งที่พบได้ทั่วไปคือรูปทรงกรวย รูปเข็ม และอื่นๆ การรวมตะกรัน การรวมตะกรันในการเชื่อมโลหะจะช่วยลดความเป็นพลาสติกและความเหนียวของโครงสร้างโลหะ และยังจะเพิ่มความเครียด ส่งผลให้เกิดความเปราะทั้งเย็นและร้อน ซึ่งทำให้ส่วนประกอบแตกร้าวได้ง่ายและเสียหาย
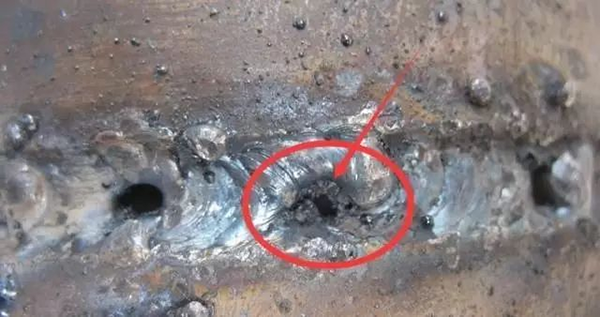
5.2 เหตุผล:
5.2.1 โลหะฐานเชื่อมไม่ได้รับการทำความสะอาดอย่างเหมาะสม กระแสเชื่อมน้อยเกินไป โลหะหลอมเหลวแข็งตัวเร็วเกินไป และตะกรันไม่มีเวลาลอยออกมา
5.2.2 องค์ประกอบทางเคมีของโลหะฐานเชื่อมและแกนเชื่อมไม่บริสุทธิ์ หากมีส่วนประกอบหลายอย่าง เช่น ออกซิเจน ไนโตรเจน ซัลเฟอร์ ฟอสฟอรัส ซิลิคอน ฯลฯ ในสระหลอมเหลวระหว่างการเชื่อม จะเกิดการรวมตัวของตะกรันที่ไม่ใช่โลหะได้ง่าย
5.2.3 ช่างเชื่อมไม่มีความชำนาญในการใช้งานและวิธีการขนย้ายแท่งไม่เหมาะสมทำให้ตะกรันและเหล็กหลอมละลายผสมกันและแยกออกไม่ได้ซึ่งเป็นอุปสรรคต่อตะกรันจากการลอยตัว
5.2.4 มุมร่องเชื่อมมีขนาดเล็ก เคลือบลวดเชื่อมหลุดออกเป็นชิ้น ๆ และไม่ละลายด้วยส่วนโค้ง ในระหว่างการเชื่อมหลายชั้น ตะกรันไม่ได้รับการทำความสะอาดอย่างเหมาะสม และตะกรันจะไม่ถูกกำจัดออกทันเวลาระหว่างการทำงาน ซึ่งล้วนเป็นสาเหตุของการรวมตะกรัน
5.3 มาตรการป้องกันและควบคุม
5.3.1 ใช้ลวดเชื่อมที่มีสมรรถนะกระบวนการเชื่อมที่ดีเท่านั้น และเหล็กเชื่อมต้องเป็นไปตามข้อกำหนดของเอกสารการออกแบบ
5.3.2 เลือกพารามิเตอร์กระบวนการเชื่อมที่เหมาะสมผ่านการประเมินกระบวนการเชื่อม ใส่ใจกับการทำความสะอาดร่องเชื่อมและช่วงขอบ ร่องลวดเชื่อมไม่ควรเล็กเกินไป สำหรับการเชื่อมหลายชั้น ตะกรันการเชื่อมของรอยเชื่อมแต่ละชั้นจะต้องถูกกำจัดออกอย่างระมัดระวัง
5.3.3 เมื่อใช้อิเล็กโทรดที่เป็นกรด ตะกรันจะต้องอยู่ด้านหลังสระหลอมเหลว เมื่อใช้อิเล็กโทรดอัลคาไลน์ในการเชื่อมตะเข็บมุมแนวตั้งนอกเหนือจากการเลือกกระแสการเชื่อมอย่างถูกต้องแล้วยังต้องใช้การเชื่อมอาร์คสั้นอีกด้วย ในเวลาเดียวกันควรเคลื่อนย้ายอิเล็กโทรดอย่างถูกต้องเพื่อให้อิเล็กโทรดแกว่งอย่างเหมาะสมเพื่อให้ตะกรันลอยขึ้นสู่พื้นผิว
5.3.4 ใช้การอุ่นก่อนการเชื่อม การให้ความร้อนระหว่างการเชื่อม และการใช้ฉนวนหลังการเชื่อมเพื่อให้เย็นช้าๆ เพื่อลดการรวมตัวของตะกรัน
6. ความพรุน
6.1 ปรากฏการณ์: ก๊าซที่ถูกดูดซับในโลหะเชื่อมที่หลอมละลายในระหว่างกระบวนการเชื่อมไม่มีเวลาถูกระบายออกจากบ่อหลอมเหลวก่อนจะเย็นลง และยังคงอยู่ภายในรอยเชื่อมจนเกิดเป็นรู ตามตำแหน่งของรูขุมขนสามารถแบ่งออกเป็นรูขุมขนภายในและภายนอก ตามการกระจายและรูปร่างของข้อบกพร่องของรูพรุน การมีรูพรุนในรอยเชื่อมจะลดความแข็งแรงของรอยเชื่อม และยังทำให้เกิดความเข้มข้นของความเครียด เพิ่มความเปราะบางที่อุณหภูมิต่ำ แนวโน้มการแตกร้าวจากความร้อน ฯลฯ
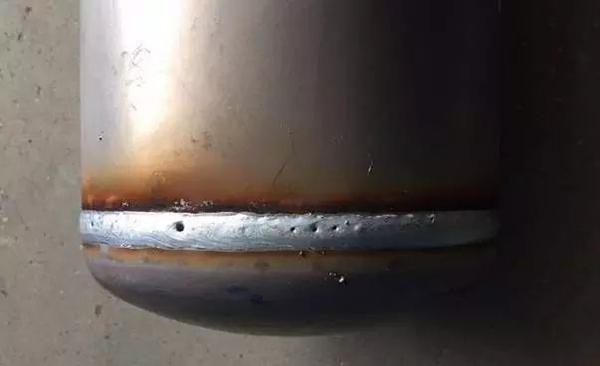
6.2 เหตุผล
6.2.1 คุณภาพของตัวลวดเชื่อมไม่ดี ตัวลวดเชื่อมมีความชื้นและไม่แห้งตามข้อกำหนดที่กำหนด การเคลือบลวดเชื่อมเสื่อมสภาพหรือลอกออก แกนเชื่อมเป็นสนิม ฯลฯ
6.2.2 มีก๊าซตกค้างในการถลุงวัสดุหลัก ลวดเชื่อมและรอยเชื่อมเปื้อนสิ่งสกปรก เช่น สนิมและน้ำมัน และในระหว่างกระบวนการเชื่อม ก๊าซจะถูกสร้างขึ้นเนื่องจากการแปรสภาพเป็นแก๊สที่อุณหภูมิสูง
6.2.3 ช่างเชื่อมไม่มีความชำนาญในด้านเทคโนโลยีการดำเนินงานหรือมีสายตาไม่ดีและไม่สามารถแยกแยะระหว่างเหล็กหลอมเหลวและสารเคลือบได้จึงทำให้ก๊าซในสารเคลือบผสมกับสารละลายโลหะ กระแสเชื่อมมีขนาดใหญ่เกินไป ทำให้แกนเชื่อมเป็นสีแดง และลดผลการป้องกัน; ความยาวส่วนโค้งยาวเกินไป แรงดันไฟฟ้าของแหล่งจ่ายไฟผันผวนมากเกินไปทำให้อาร์คไหม้ไม่เสถียร ฯลฯ
6.3 มาตรการป้องกันและควบคุม
6.3.1 เลือกใช้ลวดเชื่อมที่มีคุณสมบัติเหมาะสม และห้ามใช้ลวดเชื่อมที่มีรอยแตก ลอก เสื่อมสภาพ ผิดปกติ หรือเป็นสนิมอย่างรุนแรง ทำความสะอาดคราบน้ำมันและจุดสนิมใกล้แนวเชื่อมและบนพื้นผิวของเส้นเชื่อม
6.3.2 เลือกกระแสไฟที่เหมาะสมและควบคุมความเร็วในการเชื่อม อุ่นชิ้นงานก่อนทำการเชื่อม เมื่อการเชื่อมเสร็จสิ้นหรือหยุดชั่วคราว ควรถอนส่วนโค้งออกอย่างช้าๆ ซึ่งเอื้อต่อการชะลอความเร็วการทำความเย็นของสระหลอมเหลวและการปล่อยก๊าซในสระหลอมเหลว เพื่อหลีกเลี่ยงการเกิดข้อบกพร่องของรูพรุน
6.3.3 ลดความชื้นของสถานที่ปฏิบัติงานเชื่อมและเพิ่มอุณหภูมิของสภาพแวดล้อมการทำงาน เมื่อทำการเชื่อมกลางแจ้ง หากความเร็วลมสูงถึง 8 เมตร/วินาที มีฝน น้ำค้าง หิมะ ฯลฯ ควรใช้มาตรการที่มีประสิทธิผล เช่น แนวกันลมและกันสาดก่อนดำเนินการเชื่อม
7. ความล้มเหลวในการทำความสะอาดสะเก็ดและตะกรันจากการเชื่อมหลังการเชื่อม
7.1 ปรากฏการณ์: นี่เป็นปัญหาที่พบบ่อยที่สุด ซึ่งไม่เพียงแต่ไม่น่าดูเท่านั้น แต่ยังเป็นอันตรายอย่างมากอีกด้วย สะเก็ดที่หลอมละลายได้จะเพิ่มโครงสร้างแข็งของพื้นผิววัสดุ และทำให้เกิดข้อบกพร่องได้ง่าย เช่น การแข็งตัวและการกัดกร่อนเฉพาะที่
7.2 เหตุผล
7.2.1 ผิวยาของวัสดุเชื่อมชื้นและเสื่อมสภาพระหว่างการเก็บรักษา หรือลวดเชื่อมที่เลือกไม่ตรงกับวัสดุหลัก
7.2.2 การเลือกอุปกรณ์เชื่อมไม่ตรงตามข้อกำหนด อุปกรณ์เชื่อม AC และ DC ไม่ตรงกับวัสดุเชื่อม วิธีการเชื่อมต่อขั้วของสายรองเชื่อมไม่ถูกต้อง กระแสเชื่อมมีขนาดใหญ่ ขอบร่องเชื่อมเป็น ปนเปื้อนจากเศษซากและคราบน้ำมัน และสภาพแวดล้อมในการเชื่อมไม่ตรงตามข้อกำหนดในการเชื่อม
7.2.3 ผู้ปฏิบัติงานไม่มีความชำนาญและไม่ปฏิบัติงานและป้องกันตามระเบียบ
7.3 มาตรการป้องกันและควบคุม
7.3.1 เลือกอุปกรณ์การเชื่อมที่เหมาะสมตามวัสดุหลักในการเชื่อม
7.3.2 ลวดเชื่อมต้องมีอุปกรณ์อบแห้งและมีอุณหภูมิคงที่ และต้องมีเครื่องลดความชื้นและเครื่องปรับอากาศในห้องอบแห้ง ซึ่งห่างจากพื้นและผนังไม่น้อยกว่า 300 มม. สร้างระบบการรับ ส่ง ใช้ และเก็บรักษาลวดเชื่อม (โดยเฉพาะภาชนะรับแรงดัน)
7.3.3 ทำความสะอาดขอบรอยเชื่อมเพื่อขจัดความชื้น คราบน้ำมัน และสนิมออกจากเศษซาก ในช่วงฤดูหนาวฤดูฝน จะมีการสร้างโรงป้องกันเพื่อให้แน่ใจว่ามีสภาพแวดล้อมในการเชื่อม
7.3.4 ก่อนการเชื่อมโลหะที่ไม่ใช่เหล็กและเหล็กกล้าไร้สนิม สามารถใช้การเคลือบป้องกันกับวัสดุต้นกำเนิดทั้งสองด้านของการเชื่อมเพื่อป้องกัน คุณยังสามารถเลือกลวดเชื่อม ลวดเชื่อมเคลือบบาง และสารป้องกันอาร์กอนเพื่อขจัดสะเก็ดเงินและลดตะกรัน
7.3.5 การเชื่อมต้องมีการทำความสะอาดตะกรันการเชื่อมและการป้องกันอย่างทันท่วงที
8. แผลเป็นโค้ง
8.1 ปรากฏการณ์: เนื่องจากการทำงานที่ไม่ระมัดระวัง ลวดเชื่อมหรือที่จับสำหรับการเชื่อมสัมผัสกับการเชื่อม หรือสายกราวด์สัมผัสกับชิ้นงานได้ไม่ดี ทำให้เกิดส่วนโค้งในช่วงเวลาสั้น ๆ ทำให้เกิดรอยแผลเป็นส่วนโค้งบนพื้นผิวชิ้นงาน
8.2 เหตุผล: ผู้ปฏิบัติงานเชื่อมไฟฟ้าประมาทและไม่ใช้มาตรการป้องกันและบำรุงรักษาเครื่องมือ
8.3 มาตรการป้องกัน: ช่างเชื่อมควรตรวจสอบฉนวนของลวดเชื่อมและสายกราวด์ที่ใช้เป็นประจำ และพันให้ทันเวลาหากชำรุด ควรติดตั้งสายดินให้แน่นและเชื่อถือได้ อย่าเริ่มอาร์คนอกแนวเชื่อมเมื่อทำการเชื่อม ควรวางแคลมป์เชื่อมแยกจากวัสดุหลักหรือแขวนอย่างเหมาะสม ตัดไฟทันเวลาเมื่อไม่ได้เชื่อม หากพบรอยขีดข่วนส่วนโค้งจะต้องขัดด้วยล้อเจียรไฟฟ้าให้ทันเวลา เนื่องจากบนชิ้นงานที่มีข้อกำหนดด้านความต้านทานการกัดกร่อน เช่น สแตนเลส รอยแผลเป็นจากส่วนโค้งจะกลายเป็นจุดเริ่มต้นของการกัดกร่อนและลดประสิทธิภาพของวัสดุ
9. รอยแผลเป็นจากการเชื่อม
9.1 ปรากฏการณ์: การไม่ทำความสะอาดรอยแผลเป็นจากการเชื่อมหลังการเชื่อมจะส่งผลต่อคุณภาพระดับมหภาคของอุปกรณ์ และการจัดการที่ไม่เหมาะสมจะทำให้เกิดรอยแตกที่พื้นผิวด้วย
9.2 สาเหตุ: ในระหว่างการผลิตและติดตั้งอุปกรณ์ที่ไม่ได้มาตรฐาน อุปกรณ์เชื่อมตำแหน่งจะเกิดขึ้นเมื่อถอดออกหลังจากเสร็จสิ้น
9.3 มาตรการป้องกัน: อุปกรณ์ชักรอกที่ใช้ในกระบวนการประกอบควรขัดด้วยล้อเจียรเพื่อล้างด้วยวัสดุหลักหลังการถอดออก อย่าใช้ค้อนขนาดใหญ่เพื่อเคาะอุปกรณ์ติดตั้งออกเพื่อหลีกเลี่ยงไม่ให้วัสดุหลักเสียหาย หลุมส่วนโค้งและรอยขีดข่วนที่ลึกเกินไประหว่างการเชื่อมด้วยไฟฟ้าควรได้รับการซ่อมแซมและขัดด้วยล้อเจียรเพื่อล้างด้วยวัสดุหลัก ตราบใดที่คุณใส่ใจระหว่างการใช้งาน ข้อบกพร่องนี้ก็สามารถแก้ไขได้
10. การเจาะที่ไม่สมบูรณ์
10.1 ปรากฏการณ์: ในระหว่างการเชื่อม รากของรอยเชื่อมไม่ได้ถูกหลอมรวมกับวัสดุต้นกำเนิดอย่างสมบูรณ์ หรือวัสดุต้นกำเนิดและวัสดุต้นกำเนิดมีการเชื่อมไม่สมบูรณ์บางส่วน ข้อบกพร่องนี้เรียกว่าการเจาะที่ไม่สมบูรณ์หรือการหลอมรวมที่ไม่สมบูรณ์ จะช่วยลดคุณสมบัติทางกลของข้อต่อและจะทำให้เกิดความเครียดและรอยแตกร้าวในบริเวณนี้ ในการเชื่อม การเชื่อมใดๆ ไม่อนุญาตให้มีการเจาะที่ไม่สมบูรณ์
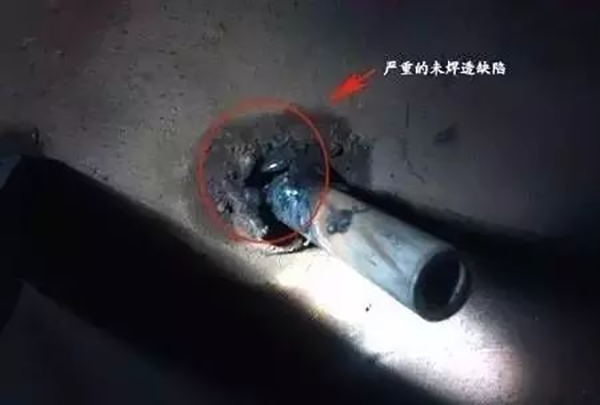
10.2 สาเหตุ
10.2.1 ร่องไม่ได้รับการประมวลผลตามข้อบังคับ ความหนาของขอบทื่อใหญ่เกินไป และมุมของร่องหรือช่องว่างของชุดประกอบเล็กเกินไป
10.2.2 เมื่อทำการเชื่อมสองด้าน รากด้านหลังไม่ได้รับการทำความสะอาดอย่างทั่วถึง หรือด้านข้างของร่องและรอยเชื่อมระหว่างชั้นไม่ได้รับการทำความสะอาด ดังนั้นออกไซด์ ตะกรัน ฯลฯ จะขัดขวางการหลอมรวมเต็มรูปแบบระหว่างโลหะ
10.2.3 ช่างเชื่อมไม่มีความชำนาญในการใช้งาน ตัวอย่างเช่น เมื่อกระแสเชื่อมมีขนาดใหญ่เกินไป วัสดุฐานยังไม่ละลาย แต่แกนเชื่อมละลาย ดังนั้นวัสดุฐานและโลหะที่สะสมของลวดเชื่อมจะไม่ถูกหลอมรวมเข้าด้วยกัน เมื่อกระแสไฟน้อยเกินไป ความเร็วของลวดเชื่อมเร็วเกินไป วัสดุฐานและโลหะที่สะสมของลวดเชื่อมไม่สามารถหลอมรวมได้ดี ในการทำงาน มุมของลวดเชื่อมไม่ถูกต้อง การหลอมละลายไปด้านใดด้านหนึ่ง หรือจะเกิดปรากฏการณ์ลมเป่าระหว่างการเชื่อม ซึ่งจะทำให้การเจาะทะลุไม่สมบูรณ์โดยส่วนโค้งไม่สามารถกระทำได้
10.3 มาตรการป้องกัน
10.3.1 ดำเนินการและประกอบช่องว่างตามขนาดร่องที่ระบุในแบบออกแบบหรือมาตรฐานข้อกำหนด
เวลาโพสต์: 28 ก.ค.-2024